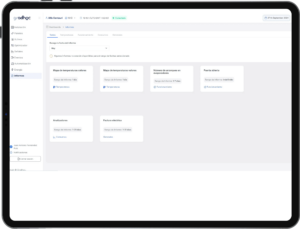
AD HOC REPORTING
Generation of predefined and ad hoc reports, both in real time and with programmable automatic sending.
Gradhoc
Predictive Maintenance
Smart refrigeration, cooler future
Request a demo or a quote
Request a demo adapted both to your sector and to your digital transformation process.
Gradhoc
Detect the failure before it occurs
Through the application of Artificial Intelligence (AI) models, the platform identifies patterns and indicators that signal the onset of potential malfunctions. As a result, events with varying levels of priority are generated, anticipating conventional alarms and triggering automatic actions.
For each of these events, the platform provides information on when they occur, whether they have been resolved or not, and a brief explanation of what is happening. Notifications can be personalized to be activated or deactivated, alerting the appropriate personnel.
This continuous analysis of the refrigeration system’s performance ensures proactive and efficient maintenance, intervening before a failure occurs.
Examples of varios events: interactive panels
Defrosting time too short; Excessive defrosting time; Ice on evaporator; Sensors out of position; Inadequate overheating reference; Air curtain gap or door open; Sensor failure; High overheating; Excessive valve opening; Missing readings; Incorrectly estimated air temperature; Lack of defrosting; Fan fault; Inadequate S4 weighting; Excessive number of defrosts; High temperature; No thermostat shutdown; Service fault; Irregular temperature…
Gradhoc
Automatic actions
Events can be automated, meaning that a specific condition (value, date, day, time) can be defined for each rule to trigger a specific action.
Automatic actions that can be performed:
Examples of automated actions dashboards
Predictive maintenance strategy
To successfully implement a predictive maintenance strategy, it is crucial to have a system that monitors the refrigeration installation to ensure maximum efficiency, predicting deterioration before it occurs and executing automatic actions to correct detected pre-faults.
Sensors collect information on physical variables and generate data to create a digital record stored and analyzed in the cloud. This data is processed to obtain normalized data (big data and deep learning).
Predictive models can forecast the temperatures of products and structures stored inside cold rooms. By utilizing mathematical equations that relate multiple variables, it is possible to optimize and extract optimal values at each moment to reduce operation costs of the installation and consequently ensure the optimal condition of the product.
Statistical models, based on neural networks, can make predictions to verify the proper functioning of the installation and, if necessary, proceed with the correction of any detected faults.
In case of detecting potential deterioration or malfunction, intelligent alarm management would be initiated, generating a completely transparent record that allows action to address the reasons for the alarm. If the absolute difference between theoretical and actual values of signals exceeds a threshold, that difference and the date it occurred will be saved.
If, in subsequent analyses, this difference increases over time, it indicates equipment deterioration or malfunction.
This analysis is conducted alongside operational rules to identify the root cause of the failure and implement a solution. This requires software that continuously analyze the installation, essential for its optimal operation and maintenance.
Gradhoc
Will you prepare for change?
Fill out the form to request a demo or a quote